Progress Toward the Intelligent Enterprise
To deliver on the promise of AI, leaders must focus their efforts on improving their organization’s culture and decision-making capabilities.
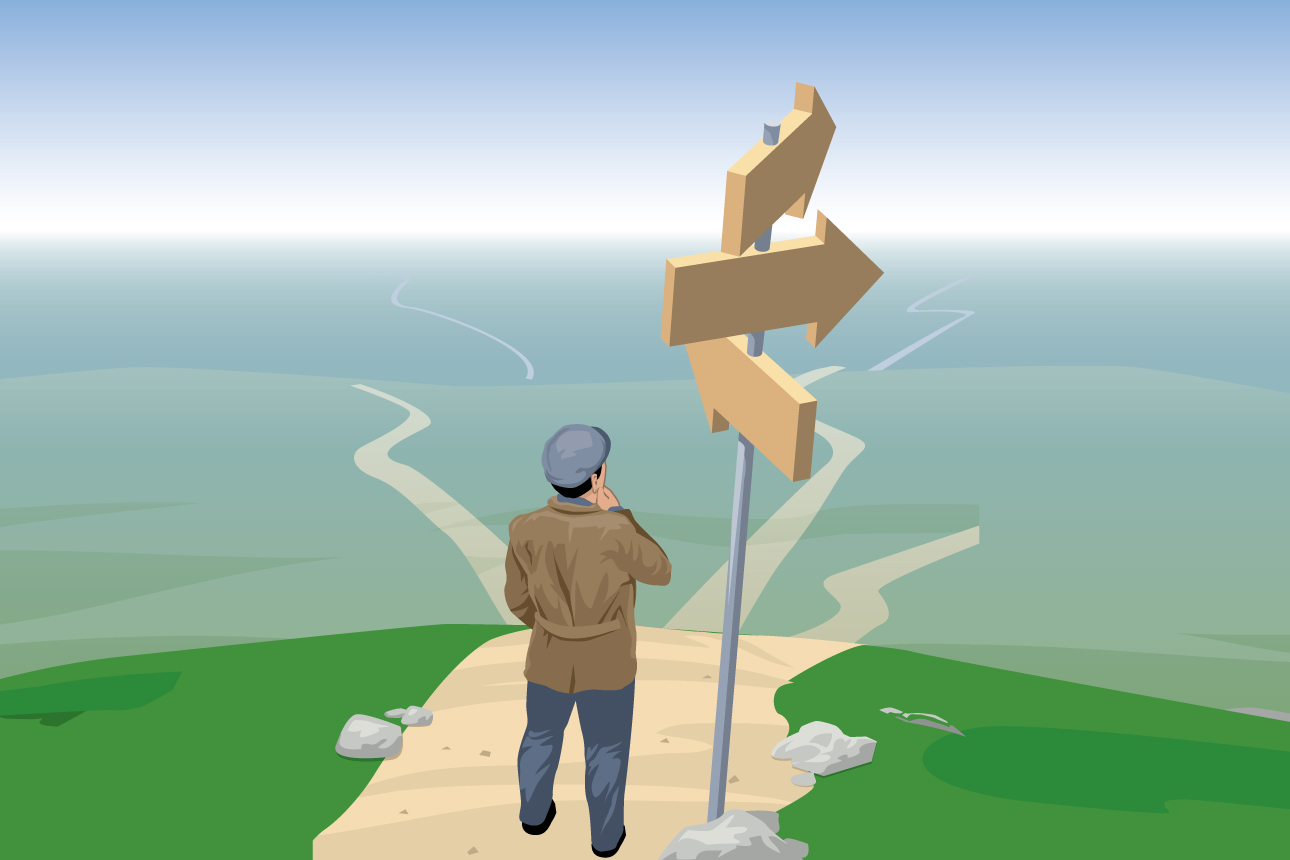
If achieving the intelligent enterprise were easy, everyone would have done it by now. The road to creating, or re-creating, a business optimized by AI to take advantage of machine-assisted decision-making at all levels of the organization is a long one.
Two key questions are, how far along are we on the path toward achieving this vision of future productivity, and are there ways organizations can improve their odds of success?
Companies are now directing billions of dollars globally each year toward AI development, yet more often than not, they’re frustrated by the lack of progress. In fact, only 1 in 10 managers who responded to a recent global survey conducted by MIT SMR and BCG could point to tangible returns. With AI investment expected to more than double to $110 billion by 2024, it’s not surprising that some leaders are asking whether that money would be better spent elsewhere in their organizations.
In one respect, they might be right.
It’s easy to do AI wrong, and it’s very hard to do it right. The organizations that are making the most significant progress on the path toward the intelligent enterprise are the ones that treat the project as a complex systems engineering problem — one that focuses more on adapting the corporate culture than it does on the technology itself.
Avoiding the Path to Frustration
Creating an intelligent enterprise is a fundamentally different undertaking than, say, moving a business to the cloud. For the latter project, one needs to do little more than call up one of the big cloud providers and perhaps hire one of any number of contractors to rewrite applications and train staff members to complete the transition. As long as you perform the due diligence and don’t cut corners on funding, IT projects tend to be straightforward.
The temptation, to the detriment of many companies, is to think of AI development in the same paint-by-number terms. After all, AI development requires IT infrastructure — the more data you have, the more computing power you need to process it. The IT component also happens to be easy to understand, and progress in the field is simple to track. Likewise, the software is more powerful than ever, with an increasing number of robust AI tools being built into common open-source programming packages.