Get Ready for the Next Supply Disruption
Companies must build the capabilities to anticipate, detect, diagnose, activate resources for, protect against, and track known and unknown-but-knowable risks.
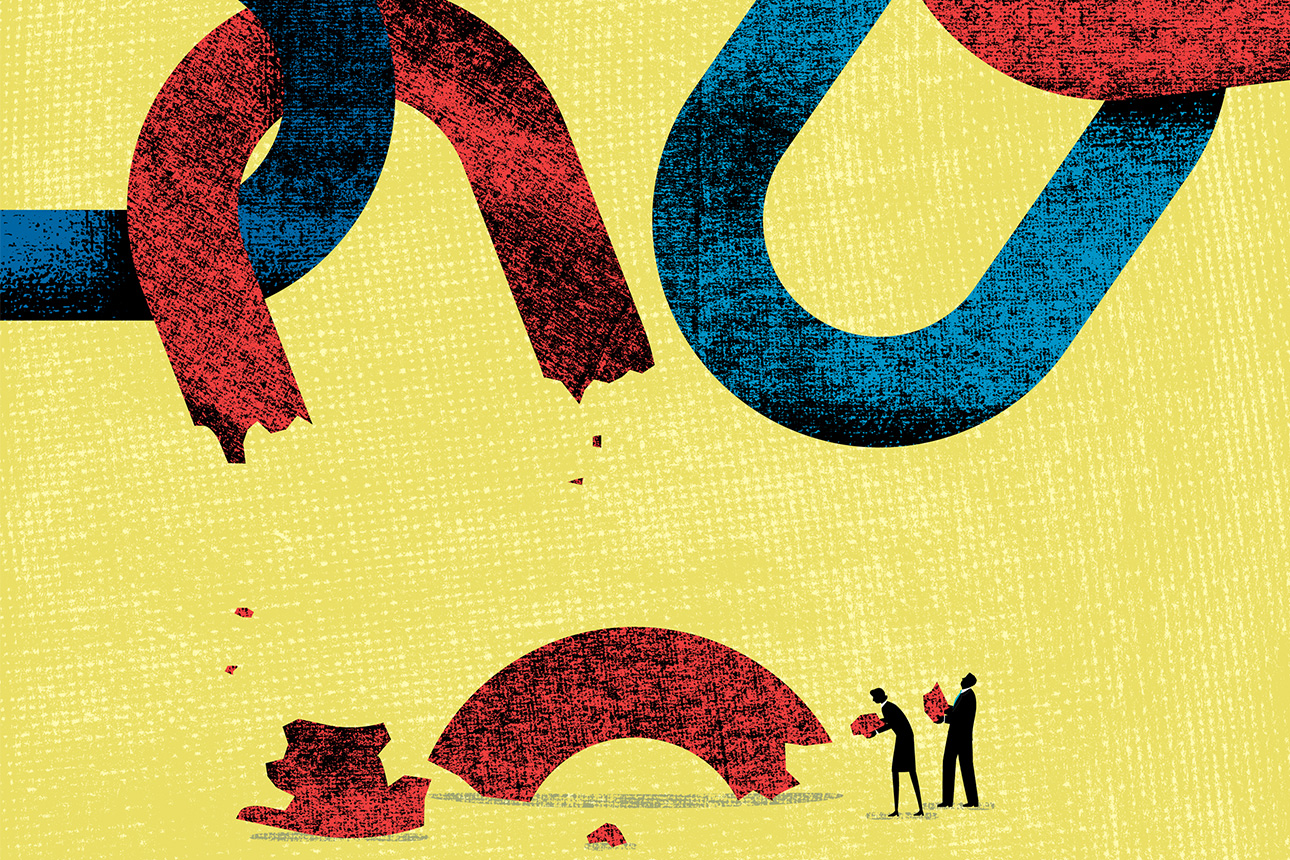
Michael Austin/theispot.com
The COVID-19 pandemic has ushered in an era of supply chain disruption and unpredictability that has severely challenged many companies’ planning and processes, and revealed how far prevailing practices are from the ideal. An MIT Center for Transportation and Logistics poll conducted online at the onset of the pandemic revealed that only 16% of organizations had an emergency response center — an established best practice for mitigating and recovering from unplanned interruptions in the physical flow of goods.1
Unsurprisingly, given the pandemic’s disruptive effects, the same poll found that the highest ambition of supply chain managers was to bolster their risk management protocols and tools. The problem with crisis-driven supply chain initiatives that are focused on protocols and tools is that they are only as effective as the ability of the organization to use them. Having that ability requires the systematic development of capabilities to manage for supply disruptions. These capabilities are combinations of people, policies, processes, and technologies that ensure companies can not only plan for and respond to known business and operating risks but also — and more importantly — manage unknown-but-knowable threats and their associated consequences.
We’ve identified six capabilities that fill this bill: anticipate, diagnose, detect, activate resources for, protect against, and track threats. Together, they constitute the ADDAPT framework, which is based on our research into how public agencies and private enterprises experience and respond to supply disruptions like the COVID-19 pandemic. In medicine, pathology is aimed at understanding the causes and effects of a disease to guide treatment. Similarly, the ADDAPT capabilities help companies understand the causes of supply disruptions and their immediate and long-term effects, in order to both respond to unfolding supply disruptions and prevent their recurrence.
References
1. Y. Sheffi, “MIT Center for Transportation & Logistics Coronavirus Response — Part Two,” Supply Chain 24/7, March 25, 2020, www.supplychain247.com.
Comment (1)
Dr. Rabindranath Bhattacharya