A Reshoring Renaissance Is Underway
Factors such as supply chain resiliency, sustainability, and geopolitical stability are just a few of the reasons companies are moving their manufacturing operations back to the U.S.
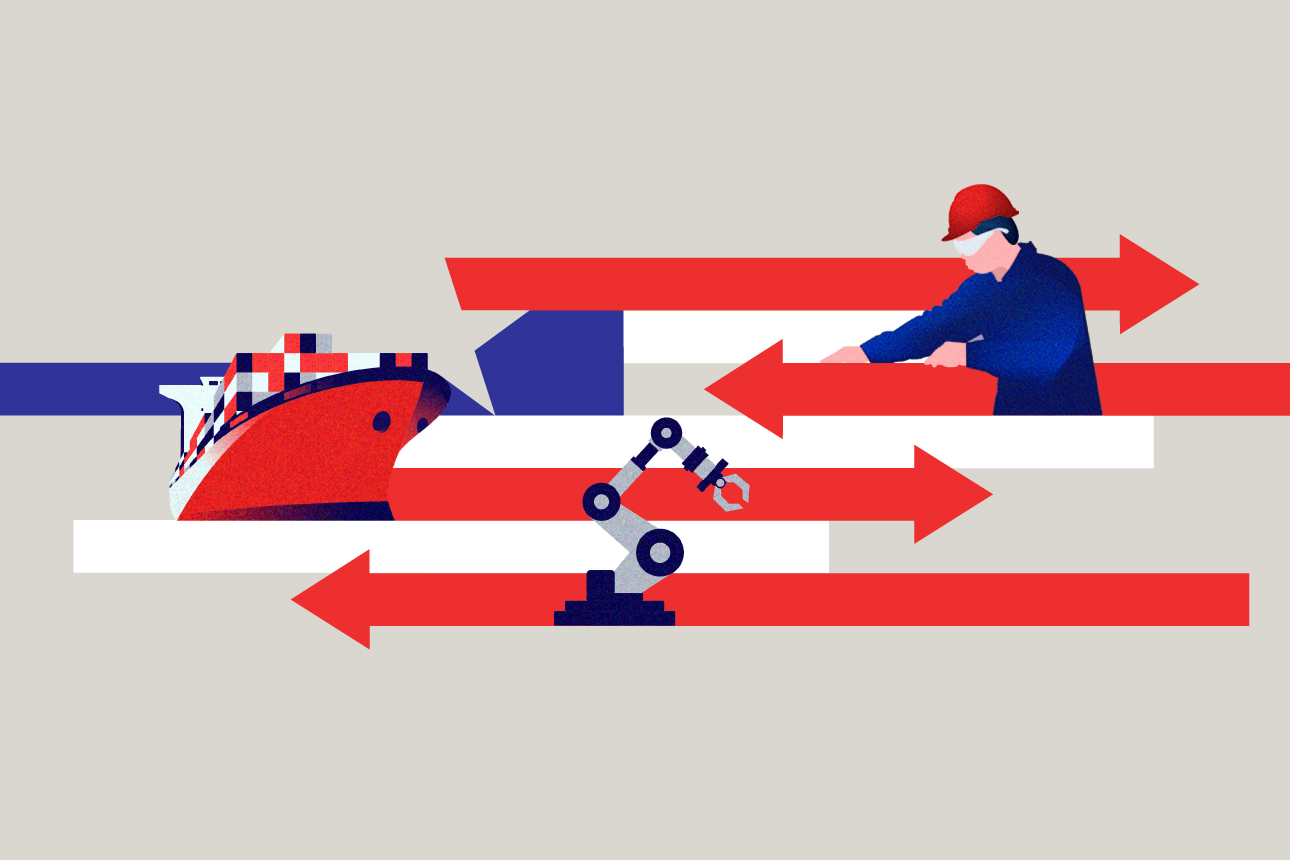
Kevin Foley/MIT SMR; Carolyn Geason-Beissel/MIT SMR | Getty Images
Companies are building manufacturing facilities in the U.S. at a pace not seen in decades. A confluence of factors is driving this trend: Amid supply chain bottlenecks, rising labor and transportation costs, U.S. tariffs on China, and geopolitical tensions, companies recognize the value of reshoring production. U.S. industrial policies favoring domestic manufacturing are also informing these decisions, including new laws seeking to address national security threats, economic disruptions, and dwindling access to key technological components. The result is an early-stage U.S. reshoring renaissance.
The question for executives is whether their companies should follow this trend. But first, it’s important to understand the trend’s scope and what’s driving it.
There have been calls for reshoring since manufacturing began sharply declining in the late 1970s, but COVID-19 marked a turning point for the C-suite. Between the first quarter of 2020 and the third quarter of 2023, executives started talking about onshoring, reshoring, and nearshoring during earnings calls and conferences much more frequently than they had previously, according to an analysis by The Conference Board.
Such talk started significantly increasing in the second quarter of 2020, as the pandemic set in globally. In the second quarter of 2022, as supply chain pressures again surged, Russia invaded Ukraine, and new federal industrial policies were enacted. Overall, instances of executives mentioning these ideas increased nearly 3,000% in just three years.
New laws also helped drive this onshoring resurgence, including the 2021 Bipartisan Infrastructure Law, the 2022 CHIPS and Science Act, and the 2022 Inflation Reduction Act. Each contains stipulations regarding the production and procurement of U.S.-made products and components that benefit companies that manufacture domestically.
Reshoring is now driving a dramatic rise in manufacturing construction activity. Companies are constructing U.S. manufacturing facilities at a higher rate than any other property type. Such spending rose to an annual rate of $114.7 billion in 2022, according to the U.S. Census Bureau — a 40% increase year over year and a 62% increase over the past five years.
This made manufacturing the fastest-growing asset category in 2022, as the average growth rate for all nonresidential buildings and infrastructure increased just 7.4% compared with 2021. And the building continues: Manufacturing spending was 74% higher in July 2023 than in the same month the previous year.